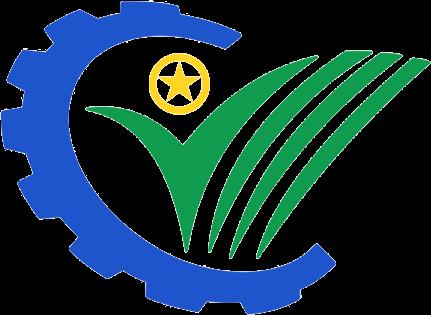
勇攀高峰 创新创效
为深入学习贯彻党的二十大精神,贯彻落实习近平总书记关于青年工作的重要思想和关于科技创新的重要论述,激发广大青年特别是企业青年的创造潜能、创新活力和创优精神,共青团中央、人力资源社会保障部联合主办了第十七届“振兴杯”全国青年职业技能大赛(职工组)——“中核杯”创新创效竞赛。
11月29日,全国决赛在南京以线上线下相结合的方式举办,经过层层选拔,来自全国29个省份、7个行业系统的261个入围项目、500余名参赛选手在“云”端巅峰对决,一较高下。经过激烈的角逐,大赛共评出金奖44个、银奖88个、铜奖129个,中国中铁共取得3金2银9铜的好成绩。
下面让我们跟随团团
一起感受创新创效的别“YOUNG”风彩!
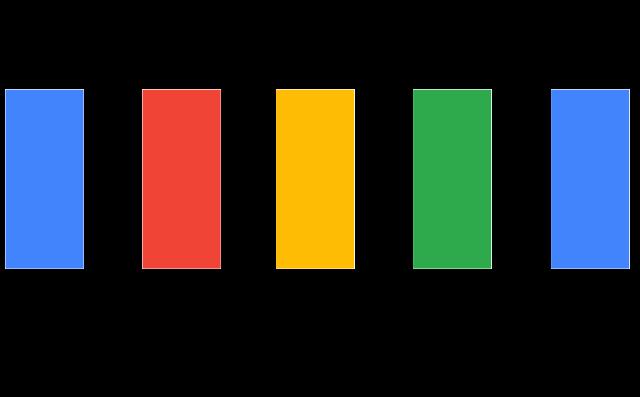
盾构机施工过程中换刀工作主要依赖人工作业,大埋深、高水压等施工环境下作业安全隐患大,易出现人员伤亡等重大安全事故,“换刀险”的国际性行业难题是制约复杂地质条件下隧道施工安全与效率的瓶颈。
项目针对盾构换刀机器人的特殊要求,研究了重载多臂复合运动机器人和兼具重载、微调和刀具快速拆装功能的末端执行机构,解决了换刀过程中的视觉导航与重载末端精确定位难题,突破了复杂工况下电液复合驱动与人机协同控制等技术,以高效安全的“机器代人”作业模式实现换刀作业。
项目创新点
快速拆装式刀具紧固机构设计
刀具引导性定位接口设计
紧凑型换刀机器人本体机构设计
兼具重载、微调和刀具快速拆装功能的
末端执行机构设计
换刀过程的视觉导航与末端精确定位技术
电液复合驱动与人机协同控制系统研究
新型刀箱已经搭载应用于13台盾构,其可靠性已经得到了验证,不仅适于机器操作,而且性能较传统刀箱也要大幅提升,得到了业主的认可。换刀机器人已于“深大城际”项目搭载应用,目前已经完成多次开仓换刀,累计更换刀具16把,平均换刀时长18.5分钟,大幅提升了施工效率与安全水平,缩短了施工工期。
盾构换刀机器人能够替代原有的人工带压换刀作业这一危险环节,同时将换刀时长由原有的≮4小时缩短为20分钟,其总体性能达到盾构机换刀技术国际领先水平。同时,能够最大限度地消除了全断面掘进机施工过程中的安全隐患,降低了工人劳动强度,提高了施工效率,减少了施工成本,具有较强的市场竞争力和应用前景。

·岩石隧道掘进机智能施工辅助控制系统开发与应用
项目围绕TBM设计与施工中“精准设计难,精细感知难,精确控制难”三大行业难题,突破了TBM岩机相互作用机理与适应性设计技术、TBM岩机状态实时感知与评价技术、多系统协同TBM智能控制与优化决策技术,岩体感知、智能掘进等核心模型准确度≥85%,滚刀磨损监测精度0.1mm,渣片识别准确率≥86%,轴线偏差±30mm以内,形成了TBM智能掘进关键技术体系,填补了多项行业技术空白,设备利用率提高10%,掘进效率提高15%,经济、社会效益显著。
①提出了基于岩机相互作用机理的TBM适应性设计方法,研发了TBM智能设计软件,首次实现了TBM从人工设计到智能设计的转变。
②研发了TBM渣片、刀盘状态、主机振动实时监测系统,提出了岩体状态融合感知方法和TBM掘进状态模糊评价方法,实现了TBM智能感知和透明掘进。
③提出了模型预测和自适应调节相结合的智能复合控制方法,研发了世界首套TBM智能施工辅助系统,实现了TBM掘进过程智能控制。
目前已在国内外15个重难点项目成功应用,避免了工程灾害发生,显著提高了掘进效率,TBM利用率由35%以下提高到45%以上,掘进速度从300~400米/月提高到500米/月以上。
项目研究成果未来将服务于国内外重大水利、交通、铁路、军工、矿山等重大工程建设,如川藏铁路、引江补汉、吉林省中部引水、国家电网抽水蓄能电站等工程,将有效拓展TBM应用场景,提高TBM地质适应性和设备利用率,降低施工风险,为TBM安全高效施工保驾护航。

·Φ7.95米世界最小直径常压换刀刀盘设计
刀盘位于盾构掘进的最前方,直接接触地层,是盾构机的“嘴巴”,长距离掘进后需对刀盘结构和“牙齿”—刀具进行体检和更换。为平衡地层压力,常规盾构刀盘需人员带压作业,环境恶劣,作业风险大,人员易患减压病等职业病。本项目开发的小直径常压换刀刀盘,人员可在大气压环境下随时检查、换刀安全可靠,针对狭窄空间开发了物料多级转运系统,配备智能在线监测平台,全方位掌握刀盘刀具状态,真正实现安全施工、便捷施工、绿色施工。
Φ7.95米的常压刀盘作为目前世界上最小直径的常压换刀刀盘, 已完成长江隧道10km的长距离安全掘进和换刀操作。随着地下空间不断开发,穿江越海项目越来越多,隧道埋深越来越大,项目水土压力越来越大,加上人们对于施工安全性的更高要求,常压刀盘的需求必然会更加广泛,15米等大直径常压刀盘技术正在稳步发展,但小直径常压刀盘版块的设计和使用经验较少,Φ7.95米小直径常压刀盘在本项目中的安全使用增加大家的信心。
未来应用于长距离天然气管道工程等直径相对较小的隧道建设中,对优化我国能源结构,促进沿线地区经济增长具有重要意义。
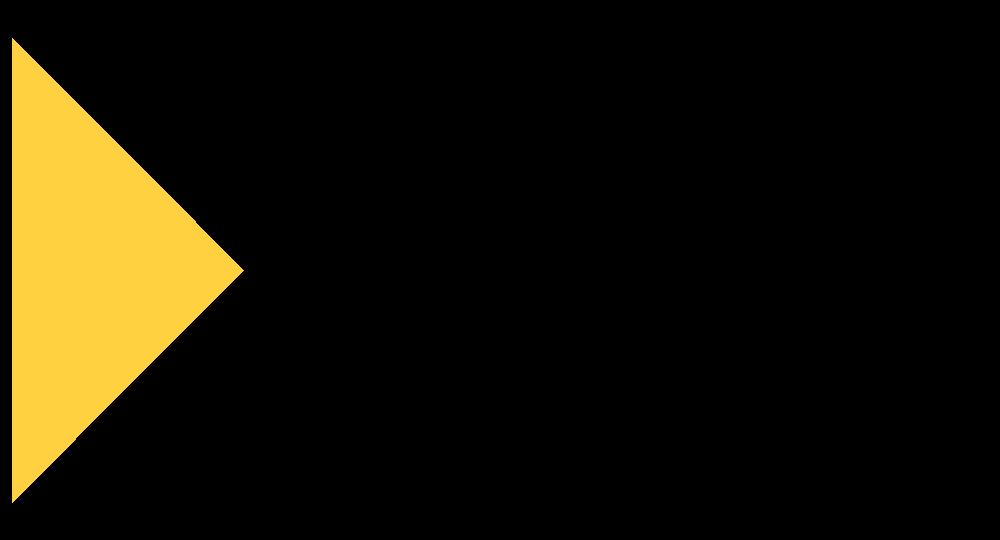

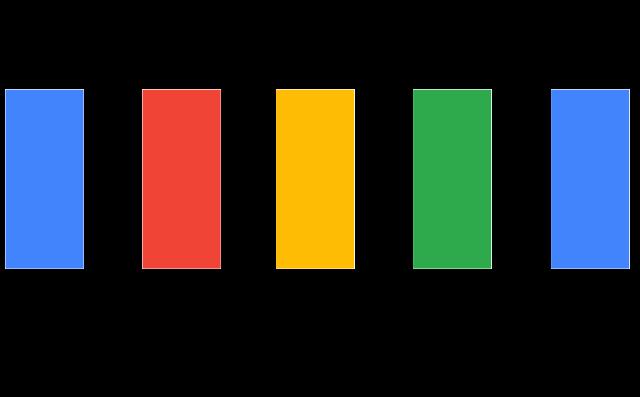
铁路预制箱梁纵向通长分布钢筋辅助安装技术
通过对铁路预制箱梁纵向通长分布钢筋传统施工方法的改进创新,研发纵向通长分布钢筋辅助安装技术,其包含铁路预制箱梁纵向通长分布钢筋辅助提料系统、免拆卸定位组件等。有效解决了铁路箱梁预制纵向分布钢筋安装施工效率低,劳动强度大等问题,大大提高了纵向通长分布钢筋安装的施工效率和机械化程度。

微小直径泥水平衡盾构机成套技术开发项目
微小泥水盾构技术的开发,弥补了国内微小直径盾构施工领域的技术空白,解决了当前城市地下复杂空间开发过程中常用工法的弊端,补足了施工过程中存在的盾构姿态控制难、管片线路成型效果差、狭小空间施工效率低等技术短板,具有双球形主动铰接主机控制技术、高密度整机集成技术、管片自动拼装技术等特点,为我国乃至世界的市政管廊、水利水电工程提供了新工法、新工艺,提高了我国重大装备在国际市场上的竞争力。
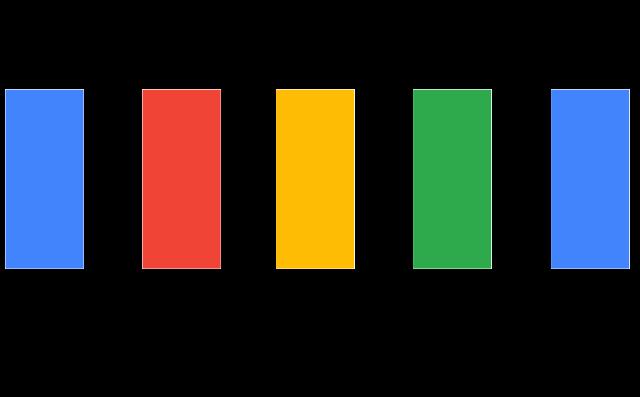
“小程序”助力“大管控”,提升企业安全管理水平
针对建筑施工企业安全管理“高危作业工序多、作业人员流动性大、流程审批繁琐、安全管控不便”等痛难点问题,以满足高危作业前置条件验收和公司后台监督管控为导向,以“信息透明化,作业规范化,申报流程化”为主线,开发高危作业安全管控系统(网页端、手机端)。系统集成了起重吊装、高空作业等高危作业管理模块,实现“申报-审核-统计-分析”全过程管理,实现安全生产人员全程参与,高危作业情况实时反馈,项目公司两级把控,能够有效提升企业安全管理水平。

预制构件牛产管理解决方案
预制构件生产管理解决方案,以BIM、云计算、物联网、移动通信、人工智能等技术为基础,以智能化设备为支撑,高度重视并发挥数据要素在推动项目数智化转型的引领作用,联动生产过程人、机、料、法、环等多生产要素,助推设计、工艺、制造协同,打造预制构件智能建造与全寿命周期数字化管理,实现以箱梁全生命周期管理为主线的全要素智能化管理,高效解决箱梁建造中信息易分散、问题难追溯、管理功效低等问题。
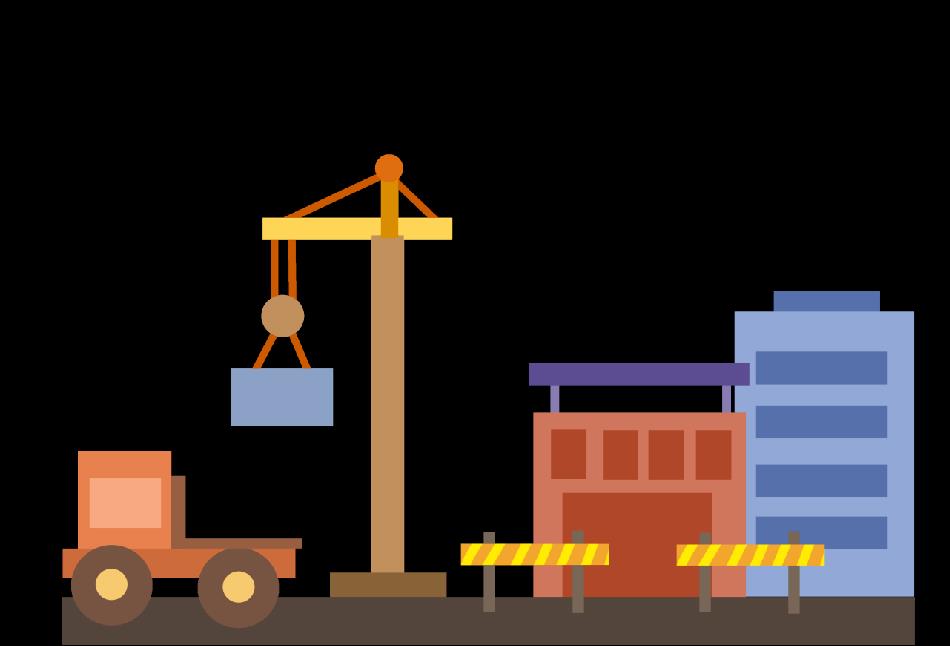

基于大数据与深度学习的盾构机智能掘进系统研究
采用理论分析、现场实测数据分析、室内模型试验、数值仿真等手段,厘清了土压平衡盾构施工各参数之间的关系,为盾构施工参数提供理论依据,并提出了施工安全评价指标。基于磨粒磨损模型提出刀具磨损预测模型,并通过现场实测进行验证,提出针对性的刀具优化配置方案。研究了装药形式对孤石预爆破裂纹发展速度的影响,归纳了爆破破碎分区范围的计算公式,形成了盾构在基岩突起和孤石群地层中施工的成套关键技术。

大直径引水管道洞内运架设备改良及配套工装研发应用
嘉兴市域外配水工程项目自进场以来针对大直径输水钢管安装工程进行市场调研、专家咨询,从工艺技术、工期指标、成本效益等多角度比选,最终确定将隧道管廊运架机进行改良作为运输工装。同时,项目充分提前分析各工序重难点,研发了自动整圆装置、自动除锈装置、二次喷浆除锈一体机等一系列配套工装,克服了有限空间内大直径钢管运输,三维空间曲线定位对接、焊接,混凝土1.7km超远距离泵送等技术难题。同步创新了工艺流程,采用钢管定位、安装、内防腐施工多点流水作业,最后混凝土基座一次性浇筑的形式,提效降本。
该项目先后获得了山东省青年职业创新创效大赛银奖、“振兴杯”全国职业技能大赛铜奖、浙江省安全质量标准化工地、“钱江杯”“南湖杯”金奖、中国中铁绿色施工科技示范工程等多项荣誉。
盾构TBM工程大数据云平台与导航掘进
盾构TBM工程大数据云平台与导航掘进项目针对盾构TBM及隧道工程生产复杂性导致的数据采集难、数据存储分析难及数据反馈应用难等,基于大数据科学、人工智能等先进技术,立足盾构TBM工程实际,开展盾构TBM多类型海量数据采集/传输技术、数据冗余存储、并行处理与深度挖掘、协同管理、风险防控及盾构TBM智能化等关键技术研究,打造了集施工/装备状态智能监测、数据分析、业务协同、风险管控、智能互联、智能掘进等多种功能于一体的行业大数据云平台,具备自主可控的大数据能力。荣获河南省科技进步二等奖、中施企协科技进步一等奖、中国中铁实用技术特等奖等。并获得软件著作权、专利、论文等60余项,具备完全自主知识产权。

时速160km架空刚性接触网系统技术及装备研究
时速160公里架空刚性接触网属于轨道交通接触网供电系统领域,为户外无备用供电设施,主要包括悬臂支撑装置、汇流排及附件、膨胀接头、分段绝缘器等产品,形成了一套完善的技术方案,解决了既有刚性接触网线路在高速运行下的拉弧、放电的难题。取得自主知识产权10项,其中发明专利3项,关键产品膨胀接头获欧洲PCT发明专利授权。经专家组评审整体技术达到国际先进水平,为我国 160km/h 及以上架空刚性接触网系统提供了新的技术装备。

铁路三维空间智能选线系统
针对铁路线路研究涉及范围广、方案多而既有选线手段存在劳动强度大、选线周期长、研究方案有限等缺点,研究了一种基于AI技术的铁路三维空间选线方法,开发了智能选线系统,可依据人工输入参数,自动在线路起终点之间优选线路方案群供设计者决策。申请2项发明专利,发表论文3篇,获四川省科技进步二等奖,第七届全国铁路青年科技创新奖。系统已在国内渝西、国外中缅等万余公里铁路项目中应用,提高工效3~5倍,经济社会效益显著。

世界最大直径岩石隧道掘进机
项目TBM最大开挖直径Φ15.084m,整机长约 182米,重量约3900吨,是世界最大直径岩石掘进机。项目具有开挖直径大、埋深大、存在软岩挤压变形、破碎等工程特点,项目团队围绕超大断面隧道TBM可靠快速掘进、减速机双速模式技术、同步拼装掘进技术等方面,进行了TBM整机关键技术研究,解决了单护盾TBM断层破碎带施工效率低、软弱围岩段卡机风险大等难题。

盘形滚刀智能制造工艺及装配研究
隧道掘进时滚刀面临的地层复杂多变,对滚刀刀圈性能要求高,现有均质刀圈制造技术无法兼顾刀圈的耐磨性及韧性。滚刀部件多,装配工艺繁杂且精度要求高,人工装配工艺无法满足批量生产需要,必须实现滚刀制造技术及装备升级。
项目研究了不同性能刀圈在不同岩性中的磨损规律,建立了刀圈性能与岩性的磨损率匹配模型。分别提出了刀圈硬度、断裂韧性与岩石岩性的匹配算法,实现了基于岩性的刀圈性能针对性设计。基于滚刀装配工艺设计了世界首条滚刀自动装配生产线,实现了滚刀装配的自动化及集成化,显著提高滚刀的装配精度及生产效率,实现了滚刀制造的智能升级。

青年,生而不凡
与祖国同奋进
与时代齐发展
中铁青年以扎实的学识
过硬的技术
在“振兴杯”的舞台上
绽放勇攀高峰的青春光彩
碰撞创新创效的青春梦想
让我们一起
为他们点赞!
校审丨支莞盈
编辑丨廖忠原(上海局)
制图丨张静果(电气化局)
来源丨中铁四局、九局、十局、隧道局、电气化局、工业、二院
扫码关注,星标团团 ↓